TECHNICAL INTELLIGENCEOur Technology
Developing highy advanced techniques through on-site innovations and industry-academic-government partherships
Tsukiboshi Manufacturing began with producing spokes for bicycles and motorcycles, and expanded their product range with long bolts, hollow rivets and precision shafts. This, along with more diversified and sophisticated customer needs, led Tsukiboshi to concentrate their efforts on developing new techniques which they have now fine-tuned to perfection. With efforts in industry-academic-government partnerships along with continued innovations on the factory floor in in-house manufacturing of machinery and equipment etc, we continually strive to make further advances in our core technique of cold forming.
Cold forming
Cold forming is a plastic processing technique in which plastic deformation is applied to room temperature materials, and a shape is formed in a die which is close to the final (net) shape. Tsukiboshi has taken this technique and is working towards achieving ‘near-net shape’ production. As long as the die can be designed to suit, it can work even for complex shapes, and a high standard of dimensional accuracy and surface smoothness can be maintained.
And since forming can be carried out without cutting the grain flow (grain texture) of the material, superior strength can be achieved. Compared with warm or hot forming, cold forming is characterized by a high degree of processing accuracy with a reduction in manufacturing steps. In addition, dies last longer, there is less scrap, and material is not being wasted, which leads to big gains in production efficiency and cost reduction. At Tsukiboshi Manufacturing, we have used our own unique innovations since our inauguration to advance cold forming techniques.
It is now a core technique which is indispensable in meeting our customers’ increasingly sophisticated and diversified needs.
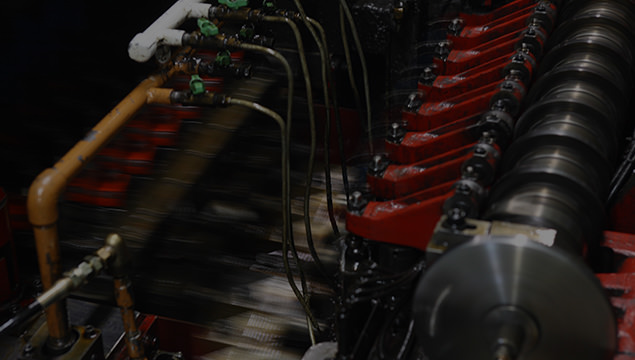
The press process
Pressing is a technique which is used to process materials into a wide variety of shapes.
At Tsukiboshi Manufacturing, by using pressing as secondary process after the core technique of cold forming, it has become possible to produce products which were previously very challenging.
Furthermore, by developing manufacturing methods which make use of the features of pressing, we aim to manufacture more complex, precision products.
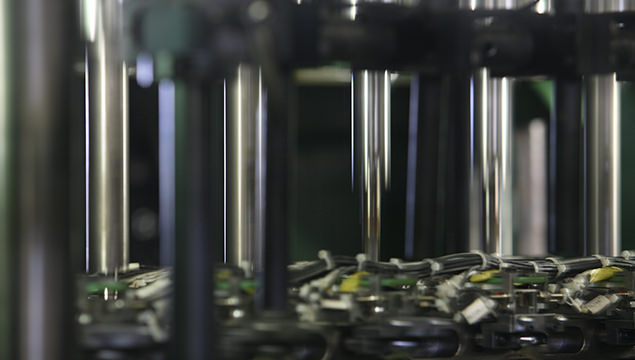
Secondary Processing
Secondary processing is a finalizing process in which near-net shape product blanks created in the cold forming process undergo precision processing. At Tsukiboshi Manufacturing, we stretch the boundaries of plastic processing by striving to get a near-net shape by making use of cold forming, thus creating a finished product for the customer while reducing waste from cutting in the secondary or tertiary processing stages. These processes highlight the limits of deformation processing.
The main processing techniques are cutting, grinding and thread rolling, and in surface reforming there is shot blasting and polishing. In addition, modifying the mechanical property of materials involves heat treatment, which we carry out by working closely with a partner factory.
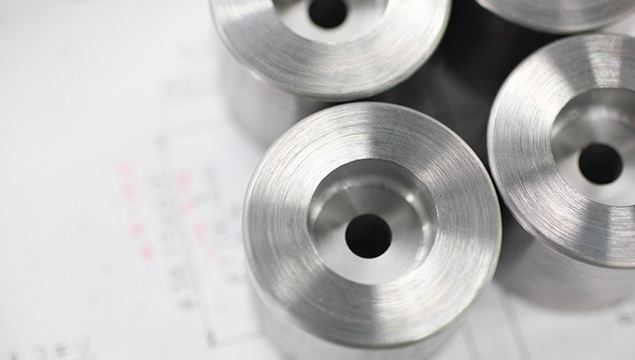
Surface treatment processing
Surface treatment processing is a technique in which the finished product is coated with a thin layer of metal or a finishing agent. Processing includes electronic plating (galvanizing, chrome plating, metal alloys etc), Geomet treatment and coating etc, and is carried out for the main purposes of improving product capability and corrosion resistance.
Through close relationships with partner factories, we are creating a structure which is not only eco-friendly with chromium free processes, but which can also cope flexibly with customer requests of any type.
For more information on surface treatment processing, go to Tsukiboshi P&P Co. Ltd.
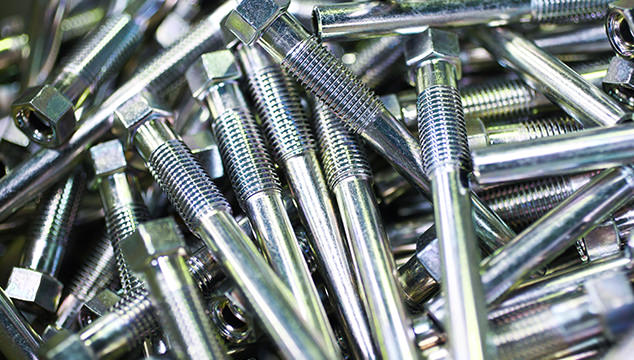